Pyrolystrator: From plastic waste to fuels and chemicals
Project description
With the growing environmental concerns of plastic waste, new methodologies are needed to reduce mankind’s impact on nature. Plastics waste is considered a huge burden on our society due to its chemical inertness. Pyrolysis, the thermal breaking of molecules, is a suitable method to “cut” these long polymer chains into suitable molecules for the production of fuels or chemical building blocks. In this project, we demonstrate this concept using a compact and mobile setup that is used to highlight the fundamental principles of polymer pyrolysis. The potential of plastic pyrolysis and the necessity to utilize new approaches to reduce CO2 emissions and lower our impact on the environment are highlighted with this demonstrator.
Advanced summary
Plastic waste is a worldwide issue with far reaching consequences to our environment, food sources and our health. Waste leaching to the environment and entering the food chain, through macro- or nano plastics, being one example of these consequences. The most effective ways to deal with this is to reduce, reuse, repair, recycle and recover plastic waste. Improving recycling techniques is necessary to reduce unavoidable waste and to create a circular economy for plastics.
Traditional mechanical recycling is currently the least energy intensive method to convert polymer waste into usable products. However, the low purity and quality of recycled polymers results in downcycling to low-end products. Mechanical recycling, therefore, only contributes to a 2% reduction of the production of virgin polymers. The main reason for the low quality of recycled plastics lies within their chemical and mechanical diversity. For example, the polymer backbone can be composed out of different monomers, each giving the final product their unique properties. The most commonly used polymers of today are PE (polyethylene), PP (polypropylene), PET (polyethylene terephthalate), PS (polystyrene), and PVC (polyvinylchloride). Furthermore, different additives are often extruded with the polymers, to obtain certain material properties, or a blend of polymers can be found in one single product. An example for this is a drinking water bottle, where the cap could be made of PP, the label consists of PVC, and the bottle itself is formed mostly from PET. It is already a challenge to remove the cap and labels on a large scale, and close to impossible to separate the protective barrier polymers from the PET that are added to prevent water damaging the polymer, with traditional mechanical techniques. Therefore, more robust and large-scale methods for the recycling of polymer waste are required. Among the options, pyrolysis has shown the required polymer waste flexibility and possibility to operate on an industrial scale. Pyrolysis is the thermal cracking, in the absence of oxygen, of polymer bonds into small molecules. Through this process, valuable products and monomers, the building blocks of the polymer, can be recovered. The use of a catalyst (catalytic pyrolysis) in the process allows fine-tuning the final product distribution and lowering operation conditions such as temperature.
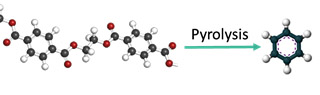
This pyrolysis demonstration unit will showcase the values of MCEC to a broad audience: tackling real world challenges and demonstrating the possibilities of recycling polymer waste. The use of different polymer blends, catalysts and its relation to the final product will be showcased. The interactive demonstrator will actively engage the audience in the process of polymer pyrolysis. In addition, the supplementary educational material will cover the topics of plastic waste recycling, circular economy, catalysis, and the pyrolysis process.